KDC
KDC drivers are responsible for delivering empty bins to grocery stores and collecting filled ones to be processed into pet food. These drivers will gather information about the bins, including their codes, contents (meat/produce), any damage, and whether they require refrigeration. This data is then transmitted back to KDC.

The Problem
At customer locations, the RFID Scanner sometimes detects incorrect barcodes in the immediate vicinity, causing inconvenience for our drivers when updating bin details. Currently, the scanner picks up all RFID codes in the area, with the DRIVE app displaying only one to the driver. If it's not the intended one, they must rescan, adjust bin positions, or input the code manually. In addition to the challenge of scanning the desired bin, the original KDC workflow involved 7 steps per bin. Considering drivers handle an average of 7 bins per stop, make about 5 stops per load, and complete 4 loads daily, this amounts to 980 steps per day. A secondary aim of this project was to streamline the process, reducing both steps and time required for bin entry.
The Value
Without the implementation of KDC Ag Logistics, the process of tracking bin information would rely on manual methods such as paper records or phone calls to Account Managers by drivers. Operations staff would then manually input this data into the TrackX systems for KDC's visibility. Given the time-sensitive nature of hauling spoiled food, which has a limited usability window for repurposing or recycling, accuracy and timeliness are paramount. KDC requires real-time knowledge of bin locations, statuses, and other relevant details. Therefore, the information entered for these bins must be accurate, easy to input, and simple for the drivers.
The Process
Research and Discovery
My self and our researcher for the DRIVE app, Ana, traveled to New Jersey to ride with drivers as they completed KDC loads. This is where we saw and heard just how much they were struggling with the workflow. We each rode with two drivers and then hosted a round table discussion with six other drivers. This allowed us to see the drivers experience, take notes, and then ask the drivers any questions we gathered from our time in the field.
After completing our research in New Jersey, we came home and set up a survey to send to all other KDC drivers. We received close to 500 responses, which further helped us develop a solid problem statement.
Workshops
01
Ideation Session
We started with our first workshop, which was the ideation session. This was about a three hour long meeting, where everyone sketched their ideas, brought them to the table, and then presented their ideas. Some people wrote their ideas, some people did very simple sketches, and a couple did high fidelity mocks. The goal of the workshop is to gather everyone's view point on how we can solve the problem. To make sure we gather as many view points as possible we have the Product Owners, Business Analysts, driver representation, Developers, UX Designers, and Product Managers. This allows us to all come together and leave the ideation session with a unified idea of how we want to solve the problem.
While each person is presenting, the others are taking notes on their likes, the challenges, and the what-ifs of each idea. A lot of the challenges come from the developers as they're seeing things that probably wouldn't be technically feasible.
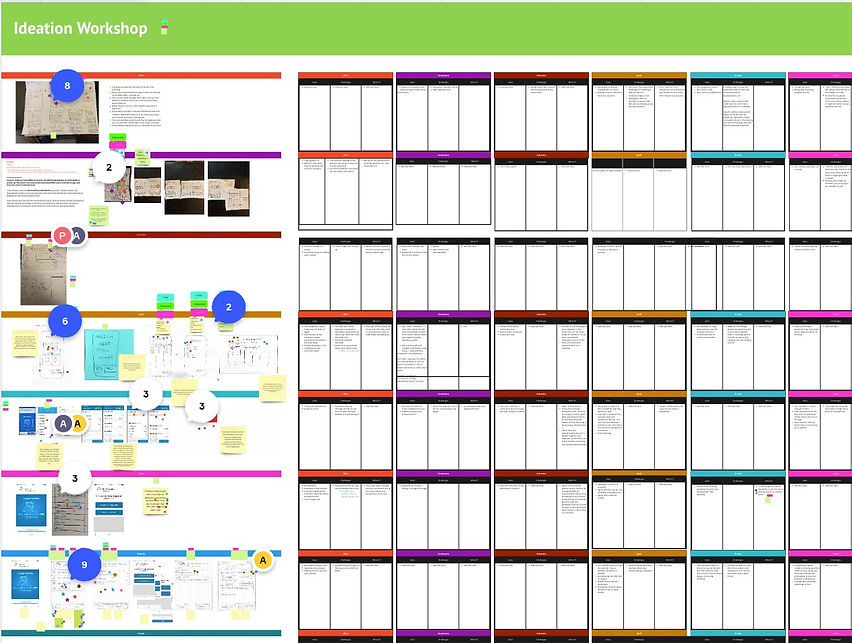

02
Prioritization Session
After the solution session, everyone votes on which ideas they liked the most. I then take all of those ideas and votes, and categorize them all. This is in preparation for our prioritization session. For the prioritization session, our goal is to narrow down the ideas based on level of effort, value to the business, and value to the drivers. The developers can really speak to the effort. The the BAs and the the transportation manager, who is representing the driver, can speak to the value it provides to the business and the driver.
After we sort through all of those items, we leave the workshops with a good idea of what the solution will look like. One of the best parts is that everyone is aligned on the direction from the start as well, which makes the process and defense of the solution much easier.
Design & Reviews
After the solution workshops, I lead two product team design reviews. The goal of these reviews is to find any gaps or missing functionality that needs to be called out in the mocks. Once we all feel confident in the designs, I present the final solution to the stakeholders. If they feel good about the solution, we move forward with development. If they have any major concerns, then I revise the mocks and schedule another stakeholder design review.
Major Design Decisions
-
When a driver scans a bin with the scanner, we show them all of the bins within their vicinity. This allows them to either only choose the one bin in front of them of select all of the bins they will need to enter details for.
-
The driver now has a page where they can see all of their selected bins and which ones still need details added for them. This allows them to easily keep track of their bins and move through them quickly.
-
We also shortened the overall steps to complete the KDC flow. We reduced it from 7 steps per bin, to only 3 steps. Which reduces the daily step count from 980 steps to 420 steps.